The Best Time to Replace Your Air Conditioner: A Complete Guide
May 5, 2025
The Best Time to Replace Your Air Conditioner: A Complete Guide
Your air conditioner is one of the most important systems in your home, especially when the temperatures soar. But like any appliance, it won’t last forever. Knowing when to replace your air conditioner (AC) can help you save money, avoid emergency repairs, and ensure your home stays comfortable year-round.
So, when is the best time to replace your AC? Let’s dive into the ideal timing, the signs that it's time for a replacement, and the benefits of planning ahead.
Why Timing Matters
Replacing your air conditioner isn’t something you want to do on impulse or during a heatwave. Choosing the right time can mean:
- Better prices and discounts
- More availability of HVAC technicians
- Avoiding emergency breakdowns
- Better planning for your household budget
Let’s explore each of these factors to help you make an informed decision.
The Ideal Season: Spring and Fall
The best time to replace your AC is during the off-season—typically spring (March–May) or fall (September–November). Here’s why:
1. HVAC Companies Have More Availability
During the summer and winter, HVAC technicians are busy responding to emergency calls. In the spring and fall, demand drops significantly. This means:
- Faster installation times
- More flexible scheduling
- Less stress for you as a homeowner
2. You Can Take Advantage of Discounts
Many HVAC companies and manufacturers offer pre-season promotions
or off-season
discounts in the spring or fall to encourage business during slower months. These deals can lead to significant savings on equipment and labor.
3. You’re Not Rushed into a Decision
If your AC breaks down in the middle of July, you’re likely to make a quick (and potentially expensive) decision just to get cool air back. By planning in advance, you can:
- Research your options
- Get multiple quotes
- Select a high-efficiency system that fits your home and budget
Signs It’s Time to Replace Your Air Conditioner
Even if your AC is still running, it may be time for a replacement. Here are key signs to watch for:
1. Your System Is Over 10–15 Years Old
Most air conditioners last 10 to 15 years with proper maintenance. If yours is in that age range, it may be approaching the end of its life—especially if you’re starting to notice more frequent issues.
2. Rising Energy Bills
Older units are less efficient, especially compared to modern models with SEER ratings (Seasonal Energy Efficiency Ratio) of 16 or higher. If your energy bills are climbing without any change in usage, your aging AC could be the cause.
3. Frequent Repairs
Are you calling your HVAC technician multiple times a year? Constant repairs can quickly add up. At some point, it’s more cost-effective to invest in a new unit rather than keep pouring money into an old one.
4. Uneven Cooling or Poor Performance
If some rooms are too hot while others are too cold—or your home just doesn’t feel comfortable—it could be a sign your AC is no longer up to the task. Newer models offer more precise temperature control and better airflow.
5. Unusual Noises or Odors
Grinding, squealing, banging, or musty smells coming from your AC are often indicators of serious mechanical issues. If these problems persist even after repairs, a replacement might be the better option.
Benefits of Replacing Before It Breaks
Many homeowners wait until their AC completely fails before replacing it. But preemptive replacement comes with some major advantages:
1. Energy Efficiency
Modern AC units are far more efficient than those made a decade ago. Upgrading can reduce your energy consumption by 20–40%, which translates into lower utility bills over time.
2. Eco-Friendly Performance
Newer models use eco-friendly refrigerants like R-410A, which are better for the environment than older types like R-22 (which has been phased out). Making the switch reduces your carbon footprint.
3. Improved Comfort
New air conditioners are equipped with advanced features like smart thermostats, variable-speed motors, and zoned cooling systems that make your home more comfortable and easier to manage.
4. Peace of Mind
Perhaps the most underrated benefit of replacing your AC before it dies is peace of mind. No more worrying about whether it will hold up through another summer—and no unexpected repair bills.
Budgeting for a Replacement
Replacing an air conditioner is a major expense. On average, a new central AC system costs $3,000 to $7,500, depending on the size of your home, the brand you choose, and the complexity of the installation.
To prepare:
- Get multiple quotes from licensed HVAC contractors.
- Ask about financing options, rebates, and tax incentives.
- Look into energy-efficiency programs in your area that may offer rebates for upgrading to high-efficiency models.
Final Thoughts: Don’t Wait for a Breakdown
While it might be tempting to squeeze another season out of your old air conditioner, that approach often leads to frustration, high repair costs, and uncomfortable days waiting for emergency service. Instead, take a proactive approach:
- Evaluate your system in early spring or late fall.
- Look for signs of aging, inefficiency, or frequent breakdowns.
- Plan your replacement during the off-season to maximize savings and minimize hassle.
- By replacing your air conditioner at the right time, you ensure your home remains cool and comfortable—and your wallet stays happy.
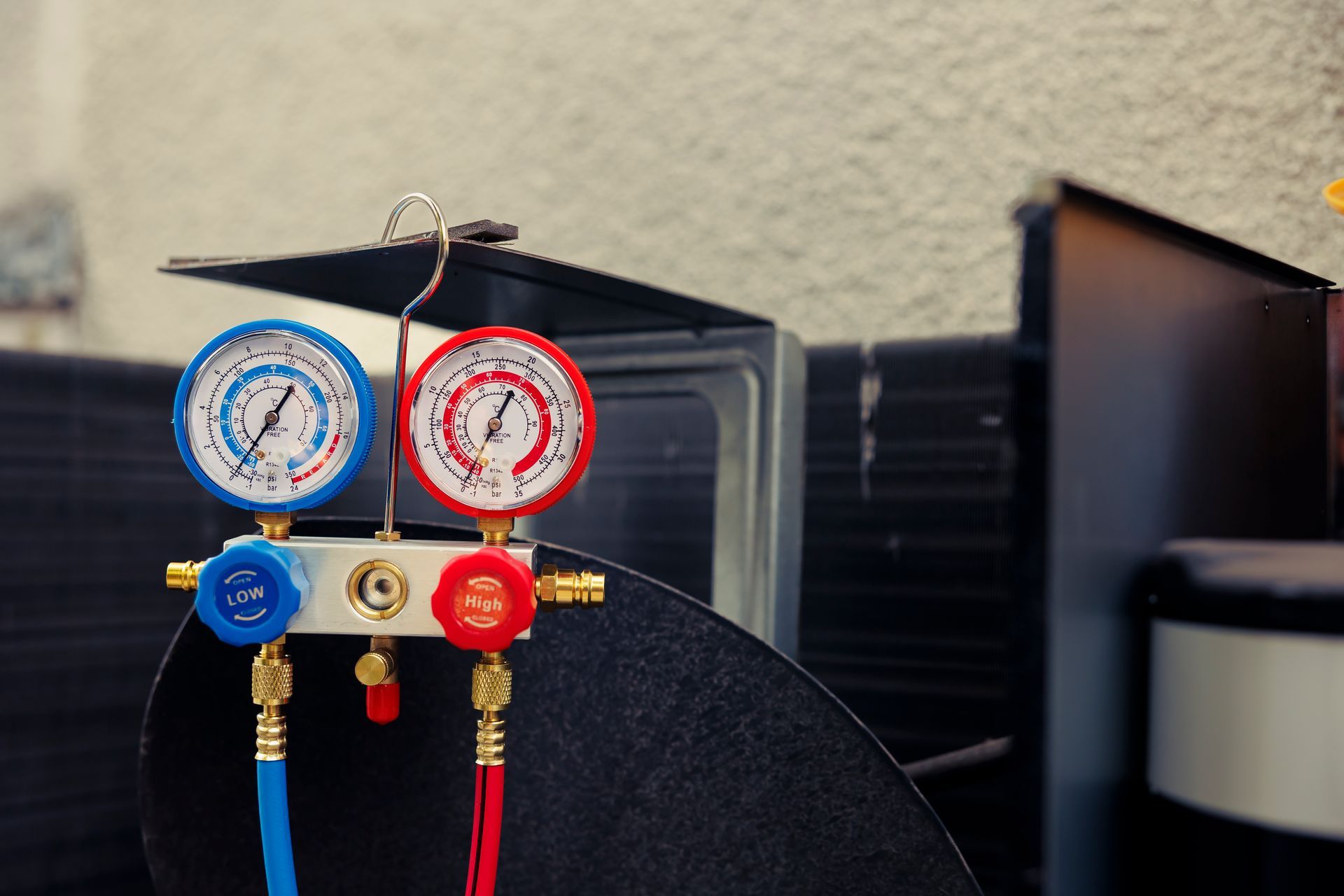
In a significant move toward reducing environmental harm and aligning with global climate goals, the U.S. Environmental Protection Agency (EPA) has introduced updated regulations targeting the use of hydrofluorocarbons (HFCs), commonly used refrigerants in air conditioning, refrigeration, and heat pump systems. These changes, building on previous rules under the American Innovation and Manufacturing (AIM) Act of 2020, are set to impact manufacturers, contractors, and consumers alike. Whether you’re in HVAC, commercial refrigeration, or just a homeowner, these new rules will likely affect you in some way. Here’s a comprehensive overview of what the new regulations involve, why they matter, and how to prepare. Background: Why Regulate Refrigerants? Refrigerants such as HFCs have long been favored for their efficiency and safety in cooling systems. However, they are also potent greenhouse gases. In fact, some HFCs have a global warming potential (GWP) thousands of times greater than carbon dioxide. As a result, efforts to reduce their use have become central to climate policy worldwide. The EPA's new rules stem from the broader goals of the AIM Act, which mandates an 85% phasedown of HFC production and consumption in the U.S. by 2036. This aligns with international efforts such as the Kigali Amendment to the Montreal Protocol. What Are the New Regulations? In October 2023, the EPA finalized a major rule titled “Phasedown of Hydrofluorocarbons: Management of Certain Hydrofluorocarbons and Substitutes under Subsection (h) of the American Innovation and Manufacturing Act of 2020”. This rule introduces several key components: 1. Sector-Based Restrictions Beginning January 1, 2025 , the EPA will enforce GWP limits on refrigerants used in specific sectors. Some examples include: Refrigerators and Freezers: Domestic fridges must use refrigerants with a GWP below 150. Stationary Air Conditioning: Most new residential and light commercial air conditioning units must use refrigerants with a GWP below 700. Commercial Refrigeration Equipment: New equipment must use refrigerants below GWP thresholds, often 150 or 300 depending on the application. These restrictions will push the market toward lower-GWP refrigerants such as R-32, R-454B, and natural refrigerants like CO₂ and propane. 2. Labeling and Reporting Requirements Manufacturers and importers will need to: Label equipment that contains HFCs or their alternatives. Report usage and sales data to the EPA. Comply with recordkeeping obligations to track HFCs and their substitutes. 3. Service Provisions While existing systems using high-GWP refrigerants can still be serviced, the EPA encourages a gradual transition. This includes: Promoting reclamation and reuse of refrigerants. Encouraging recovery during service or disposal. Implementing training and certification updates to support safe handling of flammable or mildly flammable alternatives. 4. Enforcement and Penalties The EPA has expanded enforcement capabilities and clarified penalties for noncompliance. This includes hefty fines for manufacturers, distributors, or technicians who violate phase-out rules or mishandle refrigerants. Impact on Key Stakeholders HVAC and Refrigeration Contractors Technicians and contractors will need to stay up to date on: Safe handling procedures for new refrigerants. New equipment installation practices. Updated certification and training requirements. Moreover, contractors may face increased demand for retrofits or replacements of older systems, creating both challenges and opportunities. Manufacturers Equipment manufacturers are already transitioning production lines to accommodate lower-GWP refrigerants. However, the shift may involve retooling, supply chain adjustments, and higher R&D costs. The benefit is market certainty. These regulations create a predictable framework for phasing in new technologies over the next decade. Consumers and Businesses While the cost of new low-GWP systems may be slightly higher upfront, consumers will benefit from: Improved energy efficiency in many new systems. Reduced environmental footprint. Potential incentives or rebates at the state and local levels. Commercial facilities—especially supermarkets, food processors, and cold storage operators—should prepare for more significant overhauls and investment planning. Safety Considerations with New Refrigerants Many next-generation refrigerants are mildly flammable (classified as A2L), such as R-32 and R-454B. The transition will require updates to building codes, service technician training, and ventilation standards. The EPA has coordinated with organizations like ASHRAE and UL to ensure new safety standards and performance benchmarks are in place. What Should You Do Now? Whether you’re a business owner, facility manager, or homeowner, it’s not too early to prepare for the changes. Here are some steps to take: For Contractors: Get certified or recertified on A2L refrigerants. Educate clients about the transition. Stay informed on new equipment and service protocols. For Businesses: Audit your current HVACR systems. Evaluate capital replacement timelines. Consider adopting low-GWP refrigerants sooner to take advantage of early compliance benefits. For Homeowners: If your current system is nearing end-of-life, talk to your HVAC provider about low-GWP options. Consider energy-efficient upgrades, which may qualify for tax credits or incentives. Ensure your technician is certified and uses approved refrigerants. Looking Ahead The new EPA refrigerant regulations mark a bold but necessary shift toward sustainable cooling technologies. They reflect a growing recognition that environmental stewardship and economic innovation can go hand in hand. The industry is already responding with a wave of new technologies, from ultra-low-GWP systems to natural refrigerant solutions. With proactive planning and informed choices, businesses and consumers alike can navigate the transition smoothly—and help protect the planet in the process. Final Thoughts The refrigerant landscape in the U.S. is changing rapidly, driven by environmental urgency and regulatory momentum. The EPA's new rules are not just about limiting HFCs—they're about paving the way for cleaner, safer, and more efficient cooling solutions for decades to come. Stay informed, plan ahead, and seize the opportunity to be part of a more sustainable future.
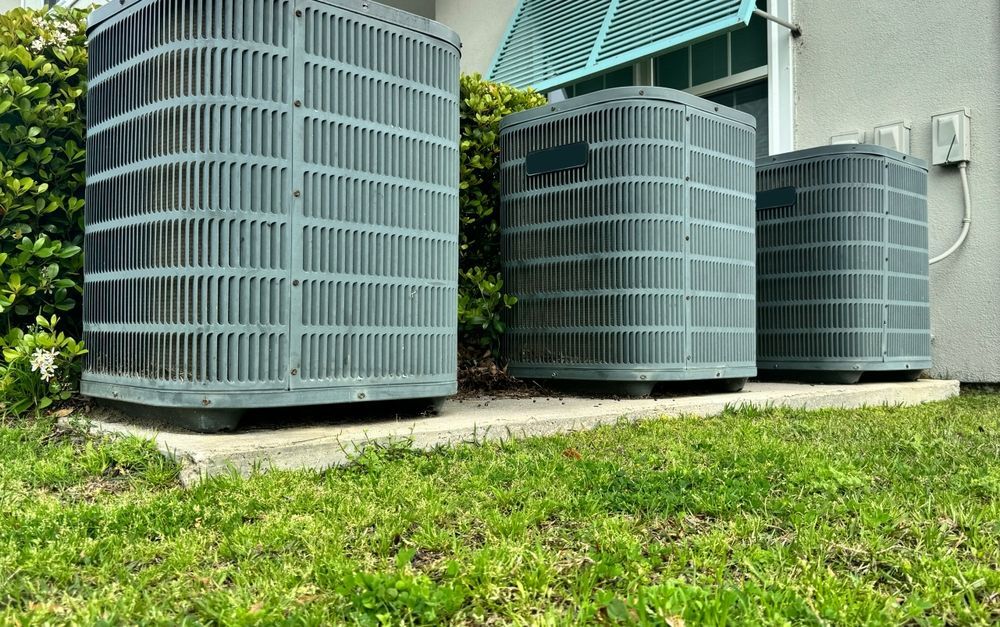
Heating, ventilation, and air conditioning (HVAC) systems are essential for maintaining a comfortable indoor environment throughout the year. Whether it’s keeping your home warm in winter or cool in summer, a well-functioning HVAC system is crucial. However, to ensure efficiency, longevity, and optimal performance, regular maintenance is a must. In this guide, we’ll explore the importance of HVAC maintenance, key maintenance tasks, and tips for keeping your system in top shape. Why HVAC Maintenance is Important Neglecting HVAC maintenance can lead to numerous problems, including increased energy costs, poor air quality, frequent breakdowns, and reduced lifespan of your system. Here are some key reasons why regular maintenance is necessary: 1. Improved Energy Efficiency A well-maintained HVAC system operates more efficiently, consuming less energy and reducing utility bills. Dirty filters, clogged ducts, and malfunctioning parts force the system to work harder, increasing energy consumption. 2. Prolonged System Lifespan Routine maintenance prevents major issues, reducing wear and tear on components and extending the life of your HVAC system. 3. Better Indoor Air Quality Dust, mold, and other airborne contaminants accumulate in HVAC systems over time. Regular cleaning and maintenance ensure that the air circulating in your home remains clean and healthy. 4. Fewer Repairs and Breakdowns Identifying and fixing small issues before they escalate can save you from costly emergency repairs and unexpected system failures. 5. Enhanced Comfort A well-functioning HVAC system ensures consistent temperature control, keeping your home comfortable regardless of the season. Essential HVAC Maintenance Tasks To keep your HVAC system running efficiently, it’s important to follow a maintenance routine. Below are key tasks that should be performed regularly. 1. Change or Clean Air Filters Dirty air filters restrict airflow, making your system work harder and reducing indoor air quality. Change disposable filters every 1-3 months and clean reusable ones according to manufacturer guidelines. 2. Inspect and Clean Ductwork Dust, debris, and mold can accumulate in air ducts, affecting airflow and air quality. Inspect and clean your ductwork annually to prevent blockages and contamination. 3. Check Thermostat Settings Ensure your thermostat is functioning properly and set at an optimal temperature for energy efficiency. Consider upgrading to a programmable thermostat for better control over heating and cooling schedules. 4. Lubricate Moving Parts Friction between moving parts can cause wear and tear, leading to inefficiency. Lubricate motors, fans, and other moving components to reduce strain and extend the lifespan of your system. 5. Inspect Electrical Connections Loose or faulty electrical connections can cause system malfunctions or pose safety hazards. Check connections regularly and tighten or repair as needed. 6. Clean the Condenser and Evaporator Coils Dirt and debris on coils reduce efficiency by hindering heat exchange. Clean both the condenser and evaporator coils at least once a year to maintain performance. 7. Check Refrigerant Levels Low refrigerant levels can indicate a leak and result in inefficient cooling. Have a professional check and refill refrigerant if necessary. 8. Clear the Drain Line Clogged drain lines can cause water leaks and humidity issues. Flush the drain line with a mixture of water and vinegar to prevent buildup. 9. Inspect the Blower Motor and Fan A malfunctioning blower motor or fan can reduce airflow, affecting system performance. Inspect and clean these components regularly. 10. Schedule Professional Maintenance While many tasks can be done by homeowners, scheduling an annual professional inspection ensures that all components are in good condition and any potential issues are addressed before they become major problems. Seasonal HVAC Maintenance Checklist Performing seasonal maintenance can help keep your HVAC system in peak condition throughout the year. Here’s a seasonal breakdown of maintenance tasks: Spring and Summer Replace air filters. Clean condenser coils. Check refrigerant levels. Inspect ductwork for leaks. Test thermostat settings. Ensure outdoor unit is free from debris. Fall and Winter Replace air filters. Inspect and clean heat exchanger. Check furnace burners and pilot light. Test carbon monoxide detectors. Inspect insulation and weather stripping. Ensure vents and registers are unblocked. DIY vs. Professional HVAC Maintenance While many maintenance tasks can be performed by homeowners, some require professional expertise. Here’s a breakdown of what you can do yourself and what’s best left to the experts: DIY Maintenance Changing or cleaning air filters. Keeping outdoor units clear of debris. Checking thermostat settings. Cleaning vents and registers. Flushing the drain line. Professional Maintenance Inspecting and repairing electrical connections. Checking refrigerant levels and detecting leaks. Cleaning and calibrating internal components. Performing safety checks on furnaces and heat pumps. Conducting a comprehensive system diagnostic. Final Thoughts Regular HVAC maintenance is essential for efficiency, cost savings, and comfort. By following a routine maintenance schedule and seeking professional inspections when needed, you can prevent costly breakdowns and extend the life of your system. Whether you handle basic tasks yourself or rely on a professional, maintaining your HVAC system ensures that your home remains comfortable and energy-efficient all year round. If you haven’t scheduled HVAC maintenance yet, now is the perfect time to do so. A little effort today can save you from expensive repairs and discomfort in the future!